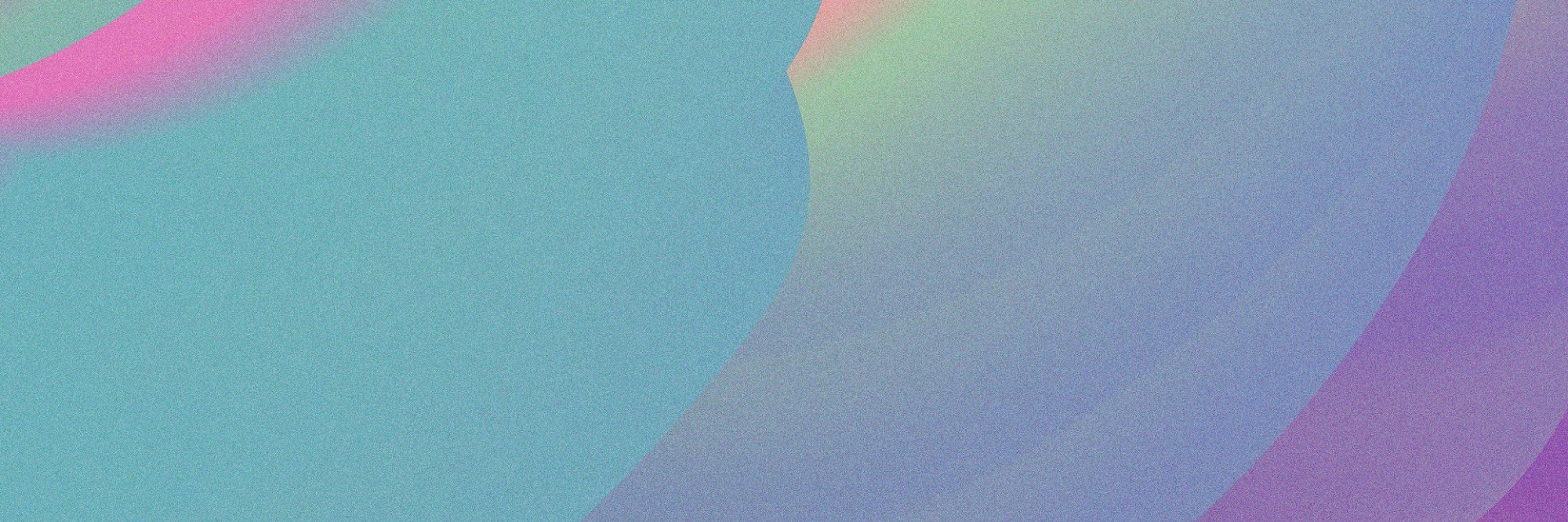
Safety stock calculator
This simple calculator will help you see how many extra items you need to keep in your inventory, in order to avoid running out of stock in case of a sudden increase in demand.
- Check your sales history to see how many items you sell on an average day, and on a really good day
- Check how much it takes for your supplier to deliver an order – on average, and in a worst-case scenario
- Fill in the fields with this data and Hit ‘Calculate’ to see how many items you need to keep as safety stock to avoid running out of products to sell
Calculate your Safety Stock.
Why your business needs safety stock and how to calculate it
If you have been in business long enough, you know that consumer demand can be unpredictable, variations in lead time occur, and suppliers can face unplanned difficulties. This is why you need safety stock to continue to fulfil orders even when there is a sudden spike in demand or if your supplier has failed to deliver goods on time.
Table of contents
What is safety stock?
Safety stock is excess inventory held by a business to protect itself against stockouts. A stockout occurs when customer orders for a product exceed the amount of inventory, and the business cannot meet demand. Stockouts can be caused by unexpected demand fluctuations, inaccurate forecasting, supply chain disruptions, working capital issues, or delayed delivery by suppliers.
With businesses investing heavily in technology and accurate demand forecasting, many adopt the just-in-time (JIT) inventory system, which allows them to order a small amount of inventory at regular intervals. This saves businesses the cost of holding stock.
However, this system doesn't work for everyone. Companies that rely on international suppliers or face difficulties in sourcing raw material, for example, can't afford to restock only when they receive an order or after they accurately forecast demand for a product. These businesses need safety stock, otherwise known as buffer stock.
How to calculate safety stock
For your business to continue to service customer orders smoothly without any unexpected delays, you need an optimal safety stock level. Very high safety stock levels will inflate your costs, while low safety stock could cause you to lose sales and hurt your business' reputation.
There is no universal formula for safety stock calculations. Production planners and supply chain managers go by instinct and experience; others calculate it based on different variables. Here we lay out some of the main methods businesses use for safety stock calculation.
But first, let's understand the terms you need to know to calculate safety stock:
Safety stock glossary
Lead time (L)
Lead time is the number of days between placing a purchase order with a supplier and receiving the ordered goods.
How to calculate average lead time
You can look at your stock receipts to calculate average lead time. If the lead times in the last four receipts were 10, 15, 12, and 18 days, the average lead time would be (10+15+12+18) / 4 = 13.75 days.
Maximum daily usage
The maximum number of units of a product sold per day.
Demand (R)
The number of items sold in a certain period of time.
How to calculate average demand (d avg)?
First, you need to determine the time frame, which is usually the time between reorders. If you reorder a product every month, then the time frame will be 30 days.
Let's assume your business is selling photo frames:
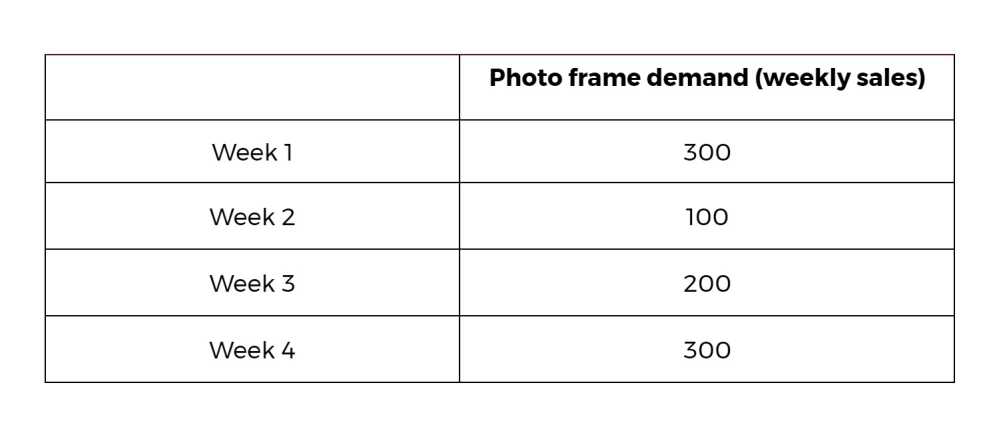
To calculate demand average, add the total sales volume and divide it by the number of days. Your demand average will be: (300+100+200+300) / 30 = 30. In other words, you’re selling 30 photo frames per day on average.
Service level
Service level is the probability that a stockout will not occur before replenishment. It takes into consideration the cost of inventory and the cost of stockouts. For example, if we say our desired service level is 95%, it means that 95% of the time we are going to be able to fulfil customer needs.
Service factor (Z)
Service factor, also referred to as the Z-score or Z-value in safety stock formulas, is your desired service level, transposed into a statistical score for easier calculation.
The easiest way to transpose a percentage into a a Z-score is to use the ‘NORMSINV’ function in Excel or Google Sheets, but you can also use the table below as a cheat sheet:
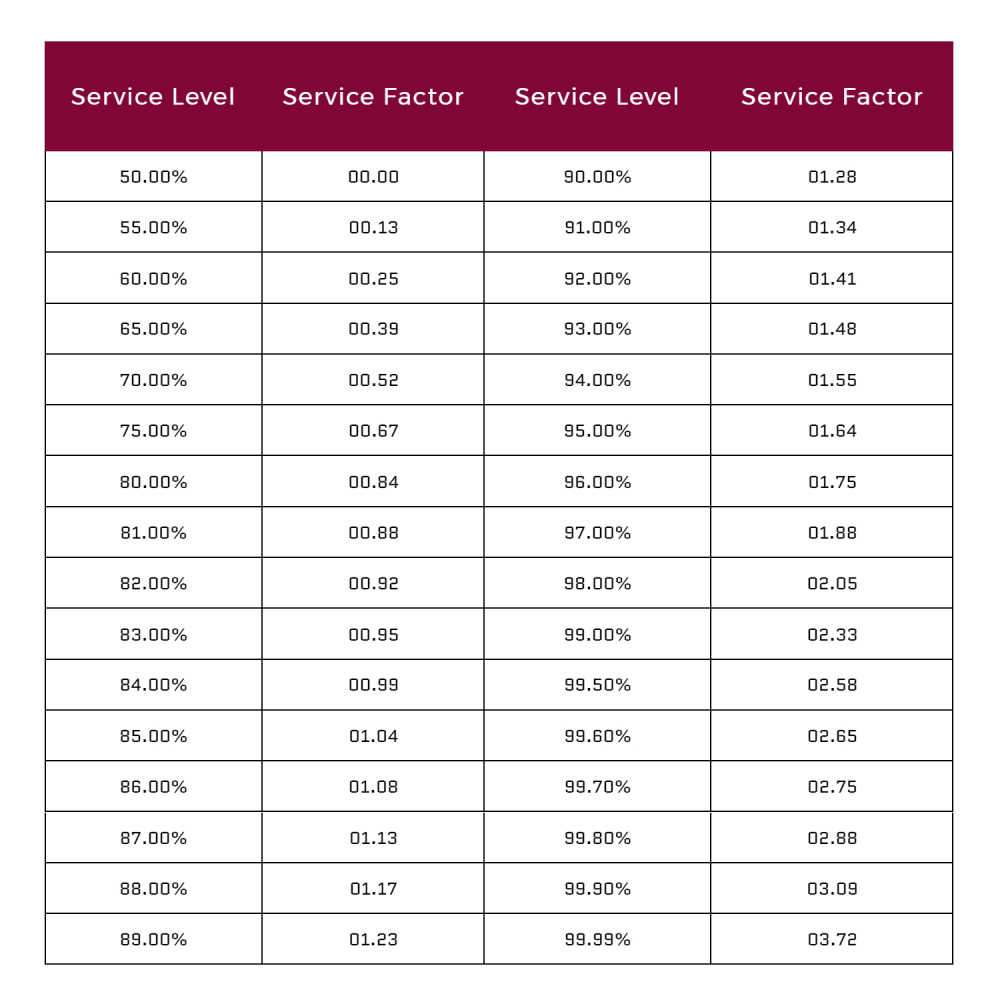
Standard deviation in lead time (𝜎dLT)
Standard deviation of lead time is the measure of variance in lead time.
How to calculate standard deviation in lead time
To calculate the standard deviation of lead time in Excel, you can use the STDEV formula.
For this formula, we need to know three key numbers which you can calculate from your order history:
1. Expected time: The expected lead time for a product
2. Actual time: The actual time it takes for the product to be delivered
3. Variation: The difference between the two
Let’s take an example. Here we are using historical data on lead times. Let's say the average lead time is 10 days and the following is the data for the last 10 orders:
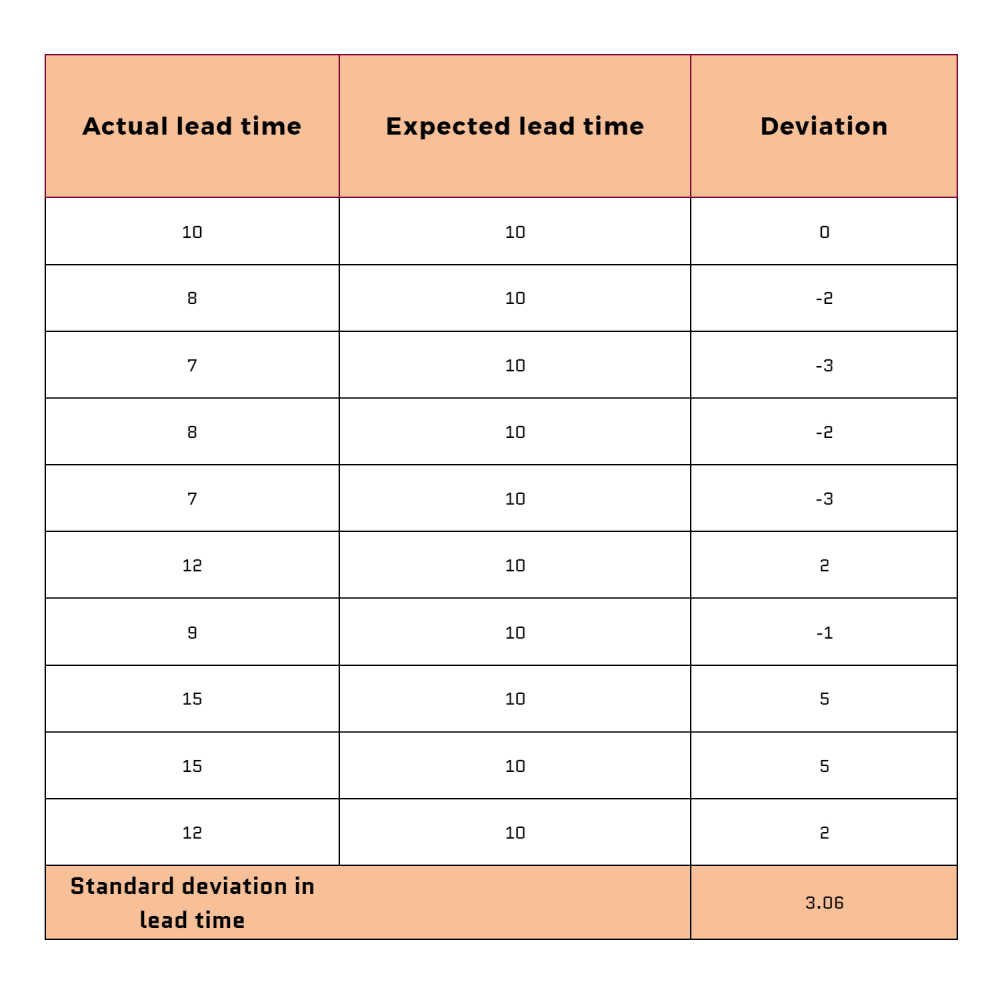
The standard deviation in this case is 3 (rounded) – calculated in Excel, using the STDEV formula.
Lead time demand (LTD) and standard deviation of lead time demand (
σLTD)
Lead time demand (LTD) is simply the total product demand over the lead time – a simple multiplication of lead time (L) by demand (R).
Lead time demand (LTD) = L x R
However, sometimes lead time is static, but demand is variable – that’s where the standard deviation of lead time demand (σLTD) comes in. Here, we multiply the square root of lead time (√L) by standard deviation of demand (σR).
Standard deviation of lead time demand (LTD) = √L x σR
Let’s go back to our photo frame vendor example and figure out how much safety stock you need, assuming the same variable demand (R) of 30 frames sold on an average day, with a standard deviation (σR) of 3. We are also assuming a constant lead time of 10 days.
This gives us a lead time demand of 300 photo frames over the 10-day lead time (10 x 30), and a standard deviation of lead time demand of 9.48 (3.16 x 3).
Safety stock calculation methods
Here are the top ways to calculate safety stock:
Basic safety stock formula
This is the traditional method of calculating safety stock – it’s useful if you already know how many days’ worth of safety stock you want to hold at a given point in time
(d avg) x Average number of days of stock
For example, if you sell an average of thirty photo frames products per day and you want to have ten days’ worth of safety stock, it will be calculated as 30 x 10 = 300 units of safety stock.
Average-max formula
Using this method, production planners or supply chain managers determine the amount of safety stock based on maximum daily usage over a period of time. This is useful when you have a very long lead time.
(Maximum daily usage x Maximum lead time) – (d avg x Average lead time)
The Heizer & Render safety stock formula
Developed by professors Jay Heizer and Barry Render – authors of ‘Operations Management: Sustainability and Supply Chain Management’ –, this method takes into account lead time as well as change in demand. This is useful when lead time is stable but demand fluctuates. This formula is based on multiplying the desired service factor by the standard deviation in lead time (𝜎dLT).
Z × 𝜎dLT
If the photo frame vendor we used in the previous examples aims for a 90% service level, with the previously calculated Standard deviation in lead time of 3, our safety stock will be 1.28 x 3 = 3.84.
The Greasley method
Safety stock calculation using the Greasley method is largely based on the Heizer & Render formula, only with the result multiplied by the average demand (d avg). This method is useful when there is uncertainty in lead time.
Greasley's safety stock formula: Z × σLT x d avg
If we take the numbers from our previous examples and assume that the standard deviation is lead time (σLT) is 5, and demand average (d avg) is 40, safety stock according to Greasley method will be: 1.28 x 3 x 30 = 115.2
Calculating safety stock with economic order quantity (EOQ)
Economic order quantity is the optimal order size for a product that a company purchases in order to minimise inventory costs.
Using this method, you can calculate the safety stock you need to reorder while considering the demand for a particular product and inventory costs such as holding, shortage, and order costs.
To calculate EOQ, you will need to know:
Holding costs – the total costs associated with holding unsold inventory
(Storage costs + Employee salaries + Opportunity costs + Depreciation costs) / Total value of annual inventory
Annual demand (D) – the total number of units sold in a year.
You can find this number by looking at your historical order data.
Order cost (S) – your total expenses associated with placing an inventory order with a supplier
Once you have all these figures, you can calculate your economic order quantity using this formula:
EOQ =(√2 x D x S) / Annual holding cost per unit
Limitations of safety stock formulas
Safety stock calculation may not always be helpful. Here are some of the limitations associated with calculating safety stock:
There are seasonal variations in demand that a safety stock formula won't account for, making it harder for seasonal businesses to calculate safety stock.
Customer behaviour can be unpredictable, especially in a world where viral social media trends inform buying decisions. For example, consider the sudden spike in demand for a fidget toy with poppable silicone blisters. It saw a meteoric rise in demand after it appeared in a viral TikTok video. In an unpredictable scenario like this, calculating safety stock isn't helpful.
Safety stock is not helpful against extreme variations in lead time. If your lead time jumps by a few months, you may still have a stockout.
Why is safety stock important in inventory management?
If you can't sell your product to a buyer, someone else will. Businesses cannot afford to lose customers or disappoint them if a product goes out of stock. These customers may replace your product with something else available on the market and never return. This is why safety stock is essential. It's a fail-safe measure that protects your business from unforeseen circumstances that may impact your inventory.
Here are the key reasons your business might need safety stock:
Inaccurate inventory forecasts
It’s uncommon for a warehouse to miscalculate inventory in the digital era. But not all businesses are equipped with modern, updated auditing tools – some businesses still rely on manual inventory checking processes. If a business takes on orders based on miscalculated inventory levels, it can end up with orders it cannot fulfil. This is when safety stock comes in handy.
It is also helpful to have safety stock in case there’s a warehouse-related emergency or products get damaged.
Supply delays
If you have waited for deliveries from suppliers or manufacturers, you know there can be variations in lead time. Having safety stock will help you keep your production cycle running smoothly in case of unexpected delays.
Demand uncertainty
Various factors impact customer behaviour and demand – prices, seasons, economic factors like employment, wages, and inflation. These are not always easy to predict. Sometimes there are additional factors that impact demand as well.
Take No-Shave November for example. The movement, which encourages men to not shave for a month, damaged the sale of shaving products but boosted beard oil sales.
Similarly, the Covid-19 pandemic forced some of the biggest companies in the world to rethink supply chains and warehousing. To battle supply chain disruptions, Amazon and other big retailers like Costco started buying large warehouses to stock products – Amazon even started chartering private cargo ships, leasing planes, and making its own containers. These are not options that small and medium businesses can afford, but they can still ensure they don't have stockouts by making smart safety stock decisions.
While demand is not always easy to predict, knowing the right amount of safety stock at the right time is helpful for all businesses.
Price fluctuations
Markets can be volatile; fluctuations in the commodities market or oil prices can impact the cost of goods and raw materials. Having safety stock can insulate your business against these sudden fluctuations and mitigate their impact on your business.
The pros and cons of having safety stock
Customer demand is hard to predict, as are supply chain disruptions. This makes having safety stock important for efficient supply chain management. It is a failsafe measure and shelters your business against disruptions.
The advantages of having safety stock
Prevents stockouts
Protects your business from an uncertain economic environment like supply chain disruptions
Prevents you from temporarily or permanently losing your customers
The downsides of safety stock
It’s tricky to have safety stock if your business deals in perishables like food items. You need some safety stock, but having too much increases the risk of spoilage and storage cost spikes.
High safety stock levels can push your holding costs higher. You have to be careful about how much safety stock you keep and factor in storage, spoilage, and obsolescence costs.
If you’re a company in its early growth phase, you should be careful about overestimating how much safety stock you need. The key reason is that you haven't been in business long enough to gauge your supply and demand accurately. If you purchase too much safety stock, you can hurt your finances.
If your business runs into money trouble or you cannot sell enough products, you should focus on what is truly hurting your business and not purchase extra inventory unless you know you can sell it.
Risks associated with safety stock
Although it’s all about minimising risk, safety stock does carry some, mostly if you miscalculate something. Here’s where most businesses make mistakes when it comes to safety stock calculation:
1. Not accounting for industry specifics
Not all businesses are impacted by the same supply chain factors or demand fluctuations. Although different businesses may use the same safety stock formula, they need to factor in variations in supply chain or reorder period, etc.
2. Not adjusting safety stock to demand fluctuations
As businesses grow, they will acquire more customers and service more orders. This means that safety stock levels need to change as well. Businesses need to review safety stock and make necessary adjustments regularly. Demand and supply aren't static either. Businesses need to regularly reevaluate supply and demand in order to maintain an optimal safety stock.
3. Not having safety stock at all
By far, the worst thing you can do is to ignore the danger of stocking out. To lower inventory costs, businesses sometimes keep safety stock levels at zero – this may sound like a good way to cut costs at first, but removing that cushion that helps manage demand fluctuations may cost your company more later on.
Safety stock FAQ
How is reorder point different from safety stock?
Safety stock is the extra quantity of product that businesses can draw from when there is a sudden surge in demand. But reorder point is the inventory level at which a business should place an order for replenishment. Both are key to inventory management and protect businesses from stockouts, sudden spikes in demand, or supply disruptions.
Reorder point calculation
When calculating reorder point, you need to factor in the lead time taken to replenish inventory so that the stock level doesn't reach zero. You can save some time by using our reorder point calculator.
Should I calculate safety stock for every product or stock-keeping unit (SKU)?
Keeping buffer stock for every product can be expensive. If you deal in hundreds or thousands of varieties of products, you should calculate safety stock for items you cannot afford to sell out of.